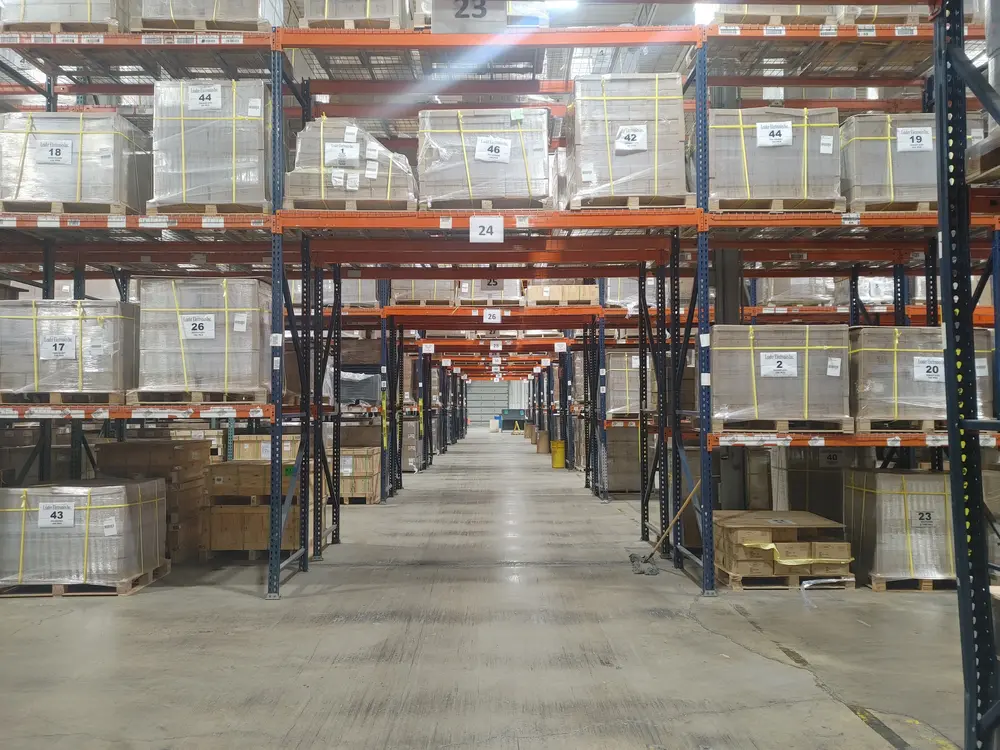
WMS Technology
A Warehouse Management System (WMS) is software that optimizes warehouse operations, inventory, and logistics.
Navigating the complexities of modern supply chains requires precision, transparency, and adaptability. At Lindner Logistics, our Warehouse Management System is designed to deliver exactly that. By synchronizing each step—from receiving inventory to final distribution—our technology helps you maintain consistent, real-time control over your stock levels, improve your operational efficiency, and adapt to sudden market changes with ease.
We’re Here for You
We offer a comprehensive range of services designed to streamline your logistics operations and drive your business forward. From warehousing and distribution to value-added services such as kitting and assembly, our team of experts is dedicated to providing the solutions you need to succeed. Contact us today to learn more about how we can help you achieve your logistics goals and take your business to the next level.
What is our WMS technology?
Lindner’s WMS Technology is a comprehensive, proprietary system designed to optimize every aspect of warehouse operations. It combines real-time inventory tracking, secure data management, and seamless integration capabilities into one powerful solution that keeps you in control of your supply chain. Whether you’re managing bulk goods or fulfilling high-volume customer orders, Lindner’s WMS Technology streamlines inbound and outbound processes, reduces manual errors, and ensures that your products move swiftly and accurately through our facilities.
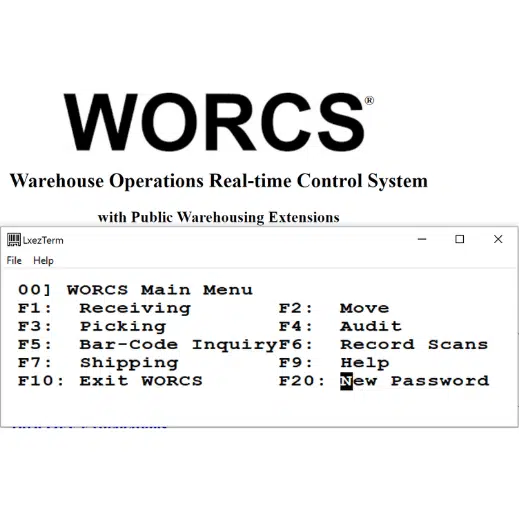
A Tailored Approach to Inventory and Distribution
No two businesses are exactly alike, which is why our technology adapts to your unique requirements. From high-volume wholesale orders to direct-to-consumer shipments, WORCS seamlessly integrates with existing processes to streamline inbound and outbound operations. Thanks to this agility, you can respond to fluctuating demand without sacrificing accuracy or efficiency.
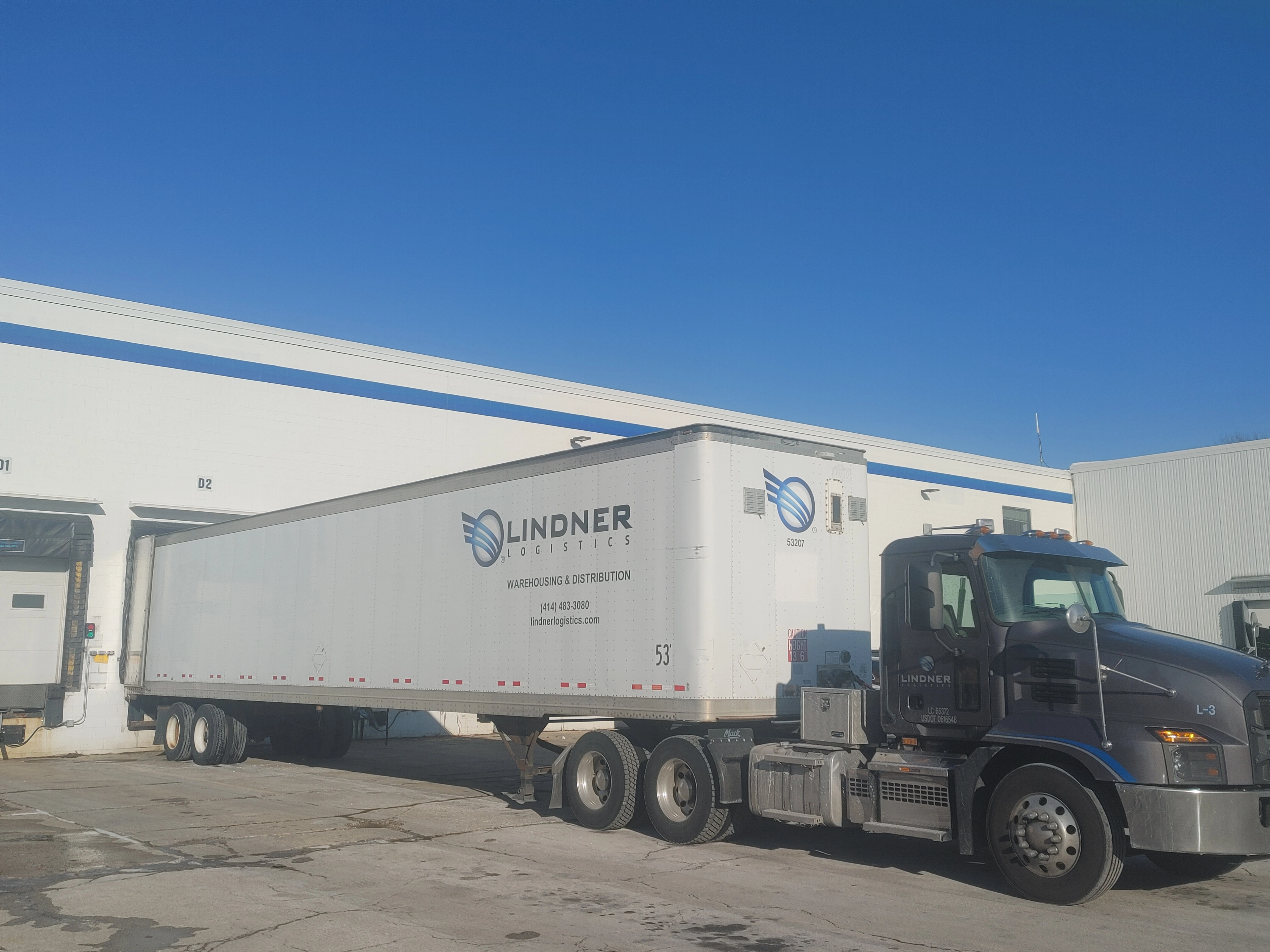
Seamless from Day One
Our experts assist with implementation and training, ensuring a smooth transition to WORCS so you can quickly benefit from reduced overhead and improved order visibility.
WMS Technology’s Key Features Key That Drive Results
Warehouse Management System (WMS) technology is designed to streamline and optimize warehouse operations. One of the key benefits of a WMS is its ability to track inventory levels in real-time, process customer orders, manage shipping and receiving operations, and generate insightful reports for performance monitoring. In this paragraph, we’ll take a closer look at some of the key features of WMS technology and how they help warehouse managers to improve their operations.
WORCS Capabilities at a Glance
Real-Time Inventory Tracking | Automated Alerts & Notifications |
Secure Role-Based Access | Seamless System Integration |
Inventory tracking
One of the core features of a WMS is its ability to track inventory levels in real-time. With a WMS, warehouse managers can monitor the movement of goods throughout the warehouse, from receiving to storage to shipping. This allows them to optimize their inventory levels, reduce stockouts, and avoid overstocking.
Order management
Another important feature of a WMS is order management. This includes the ability to receive and process customer orders, manage picking and packing operations, and track the status of orders as they move through the warehouse. By automating many of these tasks, a WMS can help warehouse managers to improve the accuracy and speed of order fulfillment.
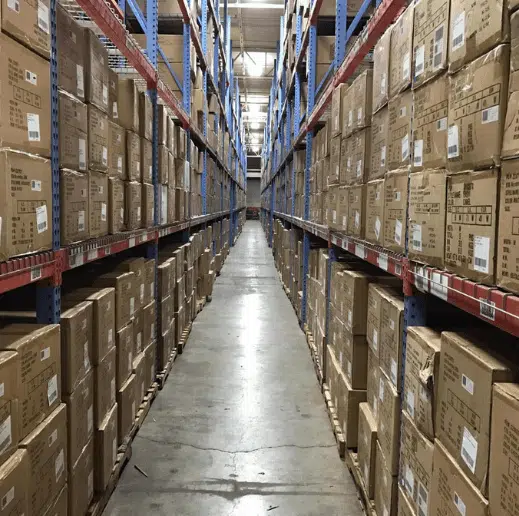
Shipping and receiving
WMS technology also includes features for managing shipping and receiving operations. This includes the ability to schedule incoming shipments, allocate storage space for incoming goods, and manage outbound shipments to customers. By automating these processes, a WMS can help warehouse managers to reduce shipping errors, improve order accuracy, and minimize the time required to process shipments.
Reporting
Finally, WMS technology includes powerful reporting capabilities that allow warehouse managers to track key performance metrics and identify areas for improvement. This includes metrics such as inventory levels, order fulfillment rates, shipping accuracy, and labor productivity. By using these reports to optimize their operations, warehouse managers can reduce costs, improve efficiency, and enhance customer satisfaction.
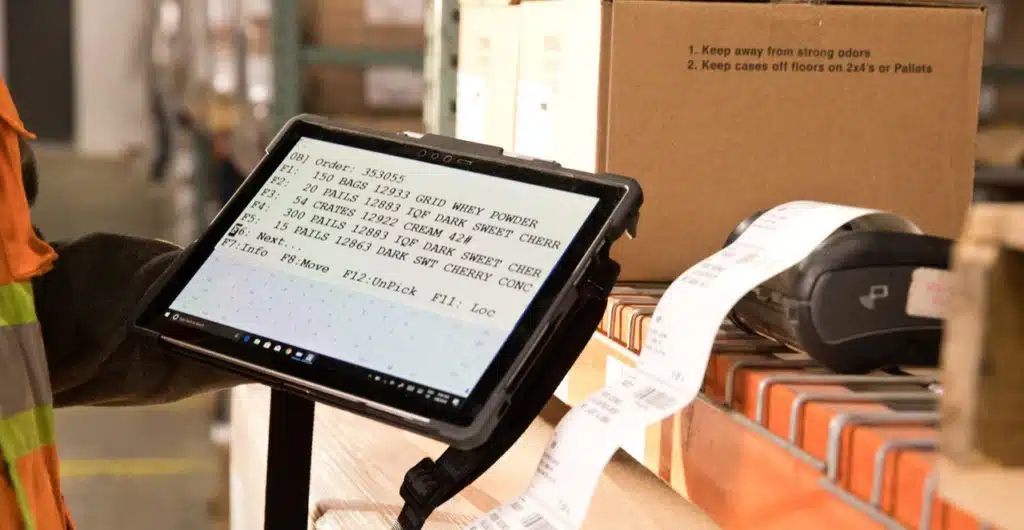
Benefits of WMS technology
A warehouse management system (WMS) is an essential tool that helps organizations to optimize their warehouse operations and streamline their supply chain management. The benefits of implementing a WMS are numerous, including increased efficiency, improved accuracy, reduced labor costs, and better customer service. In this paragraph, we will explore each of these benefits in detail to understand how a WMS can help to improve warehouse operations and enhance customer satisfaction.
Increased efficiency
WMS technology helps warehouse managers to optimize their operations, reducing the time and resources required to manage inventory, fulfill orders, and process shipments. By automating many of the manual tasks involved in warehouse management, a WMS allows warehouse managers to focus on strategic activities that add value to the business. This can lead to increased efficiency and productivity across the warehouse.
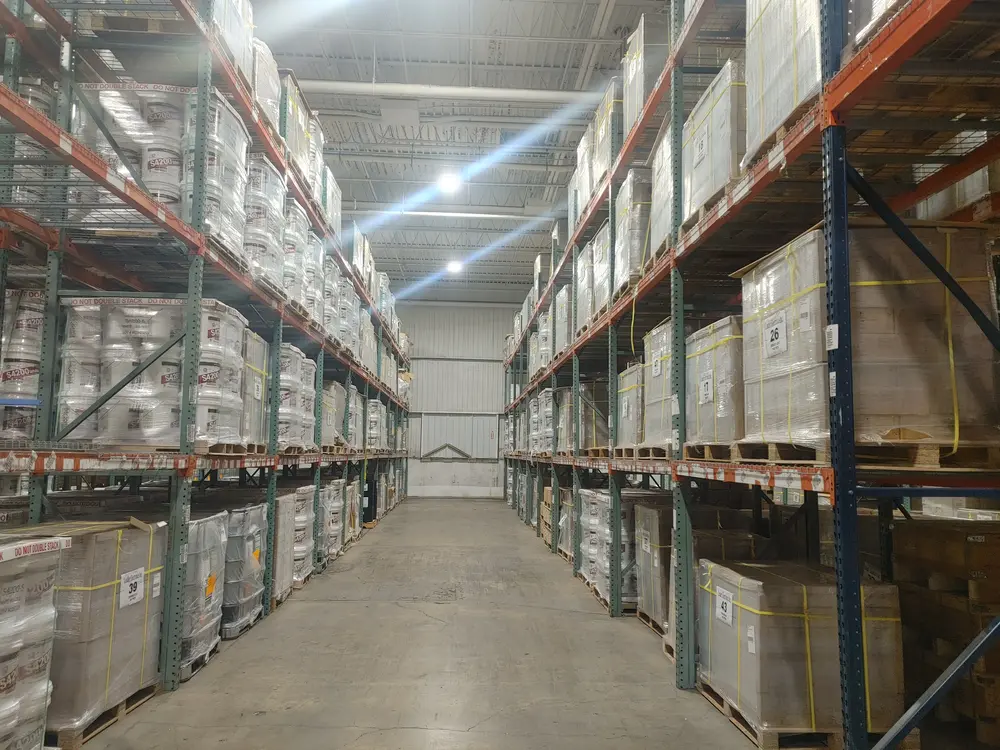
Improved accuracy
With real-time inventory tracking and order management features, a WMS helps to improve the accuracy of warehouse operations. By reducing the risk of errors and miscommunications, a WMS can help to minimize the costs associated with lost or damaged inventory, incorrect shipments, and dissatisfied customers.
Reduced labor costs
By automating many of the manual tasks involved in warehouse management, a WMS can help to reduce labor costs. This includes tasks such as inventory tracking, order processing, and shipment scheduling, which can be time-consuming and labor-intensive. By reducing the amount of time and labor required to complete these tasks, a WMS can help to reduce labor costs and improve profitability
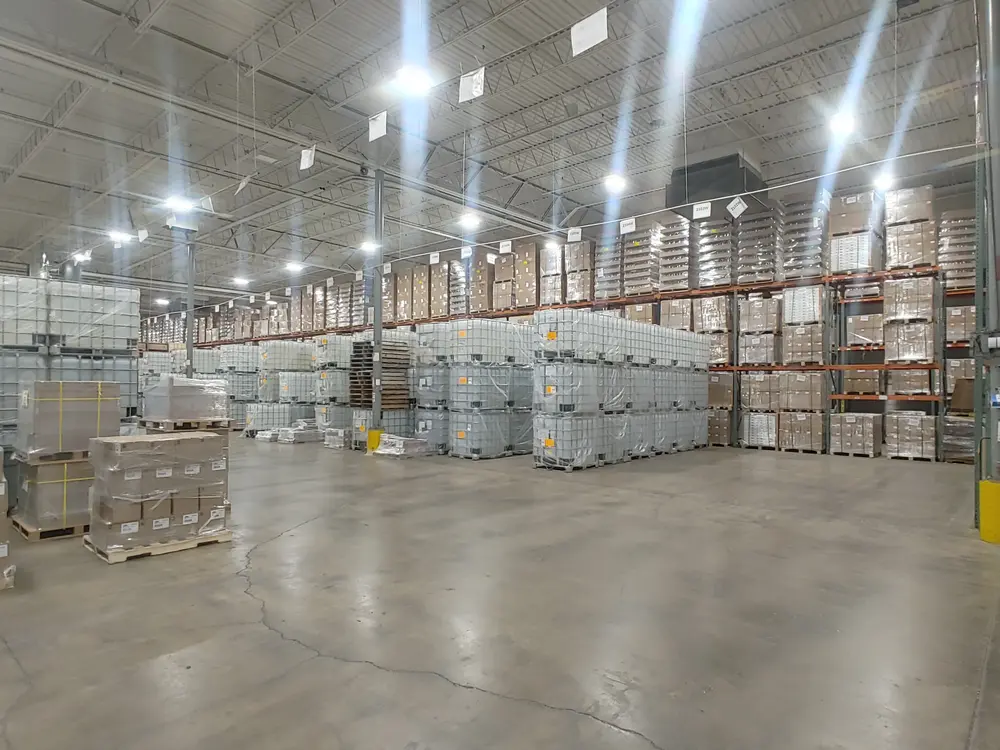
Better customer service
With improved accuracy and faster order fulfillment, a WMS can help to enhance customer satisfaction. By providing real-time updates on inventory levels and order status, a WMS can help to improve communication with customers, reducing the risk of delays, errors, and dissatisfied customers. This can lead to increased customer loyalty and repeat business.
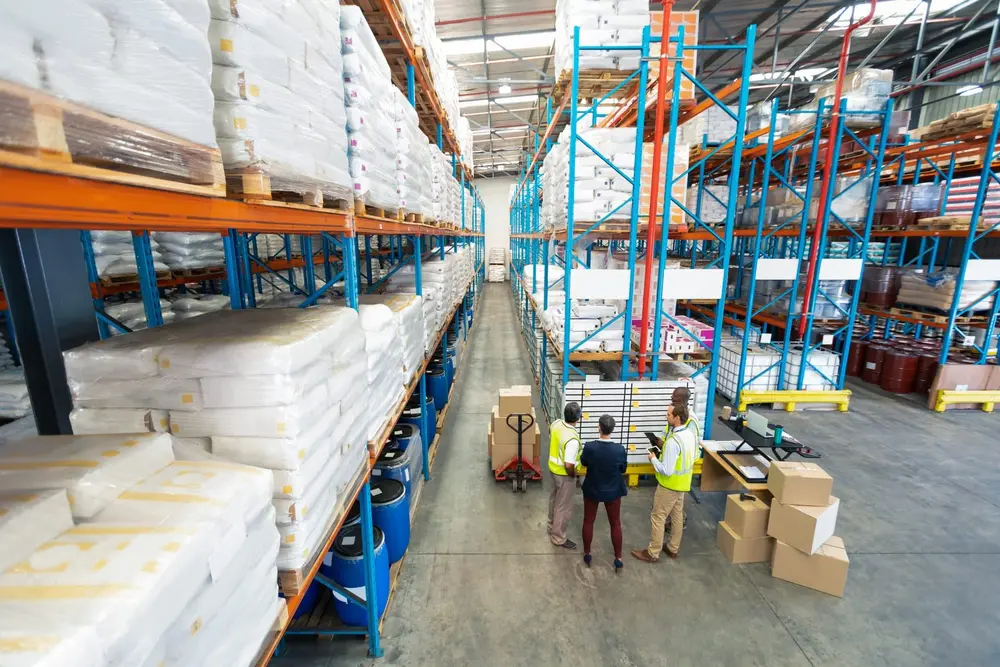
Implementation:
Implementing a WMS involves several critical steps that must be carefully planned and executed to ensure success. The first step is selecting the right software solution, followed by data migration, system configuration, and staff training. Once the WMS is implemented, it can be integrated with other systems such as ERP and TMS to create a comprehensive supply chain management solution. Let’s take a closer look at each of these steps to understand how they contribute to a successful WMS implementation.
Software selection | The first step in implementing a WMS is to select the right software for your organization’s needs. This involves evaluating vendors, reviewing features and functionality, and selecting the solution that best meets your requirements. |
Data migration | Once you have selected a WMS software solution, the next step is to migrate your existing data to the new system. Transferring data such as inventory levels, customer orders, and shipping information from your existing system to the new WMS. |
System configuration | After the data has been migrated, the next step is to configure the WMS system to meet your organization’s needs. |
Staff training | Once the system is configured, the next step is to train your staff on how to use the new WMS. This includes training on the new workflows, system functionality, and best practices for warehouse management. |
Testing and deployment | After staff training is complete, the final step is to test the system and deploy it in a live environment. Once the system is live, it’s important to monitor performance and address any ongoing issues to ensure that the WMS is running smoothly. |
Integration | Discuss how a WMS can be integrated with other systems, such as ERP (Enterprise Resource Planning) and TMS (Transportation Management System), to create a comprehensive supply chain management solution. |
WORCS
We are committed to delivering the latest and most advanced technology solutions to our customers. We recognize that today’s competitive business environment requires a high level of efficiency and accuracy, which is why we have developed our own proprietary Warehouse Operations Real-Time Control System (WORCS). This state-of-the-art system allows you to have complete control over your inventory by providing real-time data that can be accessed from anywhere, at any time. With seamless online ordering and advanced routing and picking capabilities, we make it easy to manage your inventory and streamline your operations. Our system also provides advanced ship notices, giving you full visibility into your supply chain and enabling you to proactively address any issues that may arise. At our company, we are dedicated to leveraging technology to enhance our customers’ experience, improve their bottom line, and help them stay ahead of the curve in an ever-evolving marketplace.
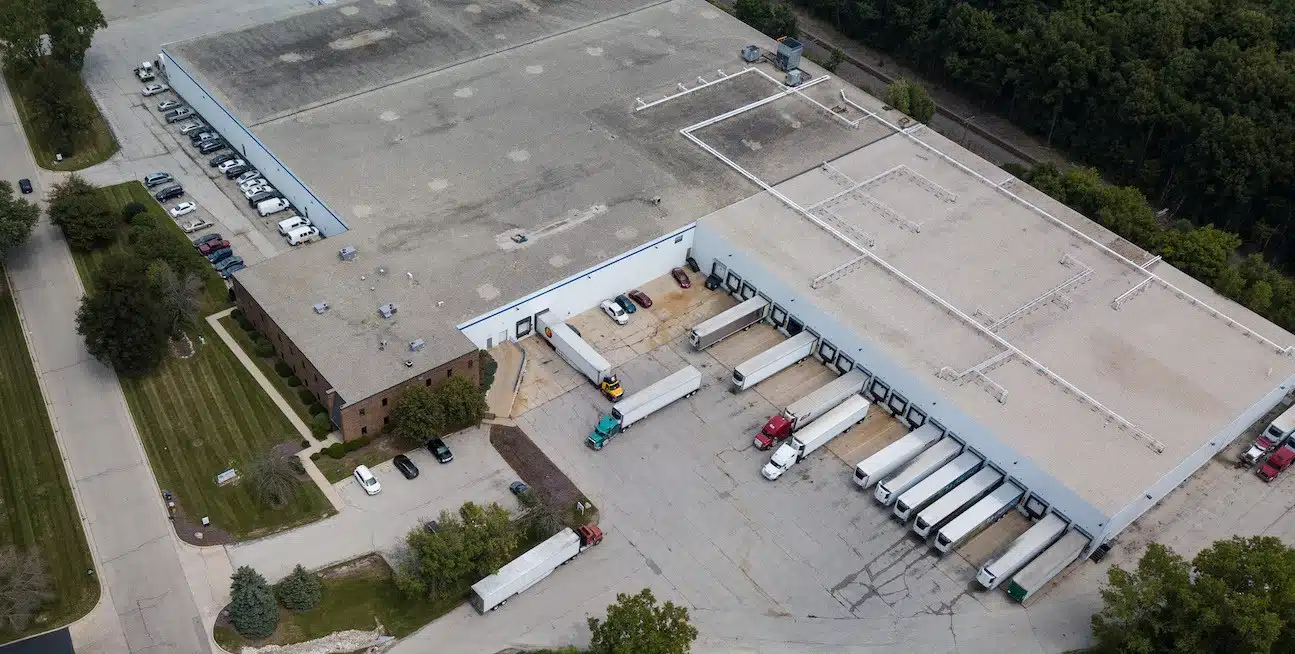
Data Security
We know that data security is a top priority for our customers. With the rise of cyber threats, it’s essential that businesses take proactive measures to safeguard sensitive data. That’s why we have implemented a comprehensive approach to data security that is designed to protect your data at every level. From our physical infrastructure to our software applications, we have implemented a range of security measures to ensure that your data is secure at all times. Our dedicated IT staff monitors our systems around the clock, proactively identifying potential threats and taking swift action to mitigate them. We also use advanced encryption techniques to secure all data transmissions and limit account access to only those who require it. By taking these and other measures, we can provide our customers with the peace of mind that comes with knowing that their data is protected against unauthorized access, theft, and other forms of cybercrime.
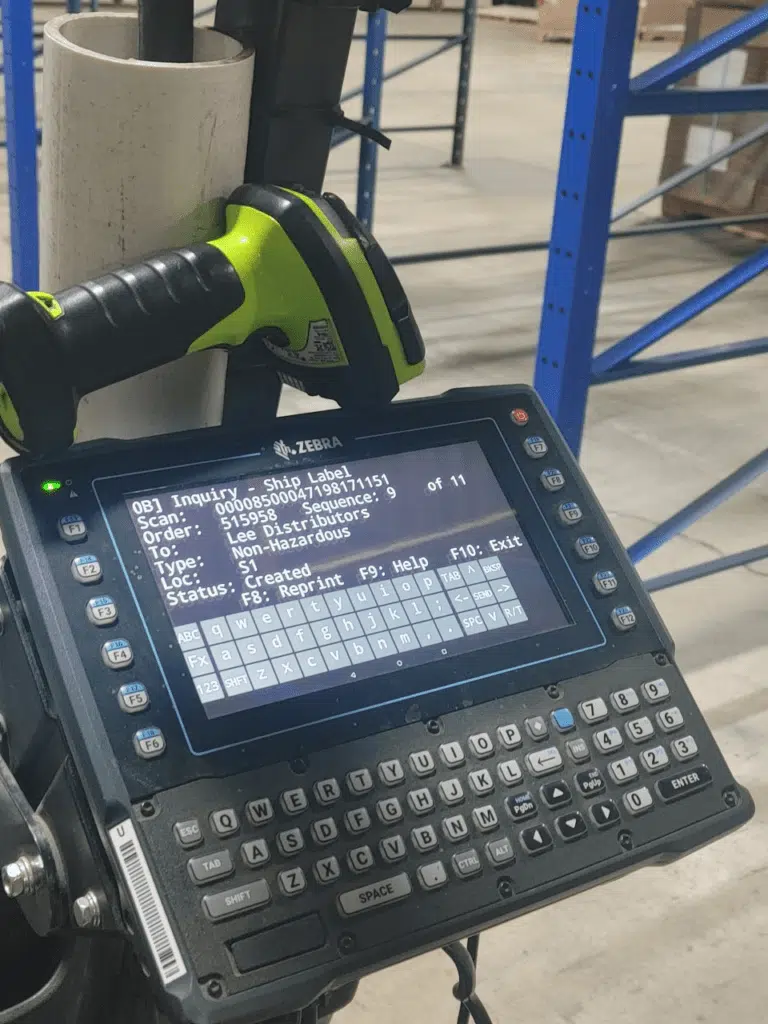
Our Investment in Technology Impacts Your Supply Chain
At Lindner Logistics, we are dedicated to providing our customers with the best possible logistics solutions to help them save time and money while also providing peace of mind. We recognize that logistics can be a complex and challenging process with many variables that can impact the success of the supply chain. That’s why we have invested in the latest technologies, including automation, transparent communication, and advanced software solutions, to help simplify the process and break it down into manageable steps.
By integrating automation into our logistics processes, we can streamline workflows and eliminate manual tasks, such as data entry and order processing, that can be time-consuming and error-prone. This helps to increase efficiency and productivity, allowing us to process orders faster and reduce delivery times, ultimately resulting in cost savings for our customers.
We also understand the importance of transparent communication in logistics, which is why we have implemented systems that provide real-time updates on order status and inventory levels. This allows our customers to stay informed about the progress of their orders, which helps to reduce delays and prevent errors. Additionally, our advanced software solutions help us to identify and address potential problems before they occur, ensuring that our supply chain operates smoothly and without interruption.
Overall, our commitment to integrating automation, transparent communication, and advanced software solutions into our logistics processes helps to simplify the complex logistics system and break it down into manageable steps. This results in a successful and efficient supply chain that meets the unique needs of our customers.
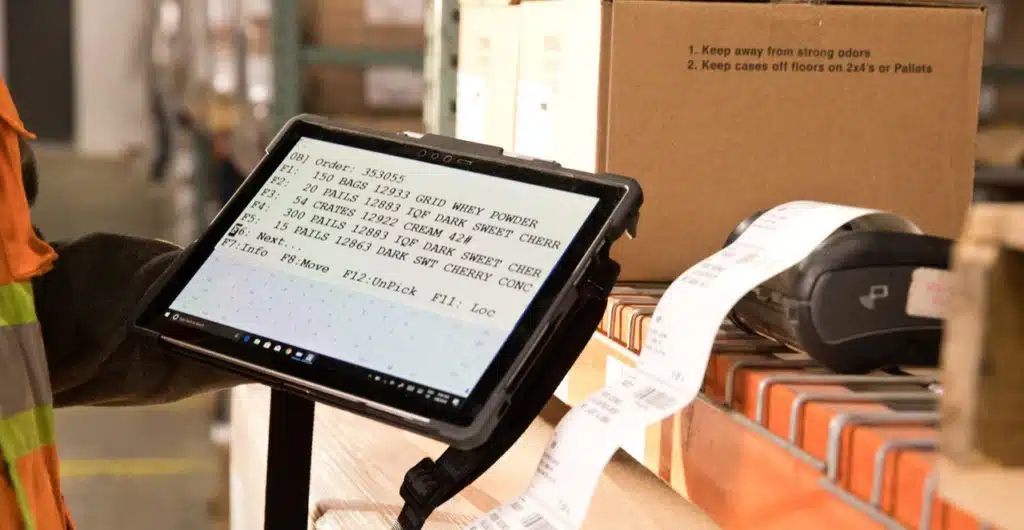
Related news
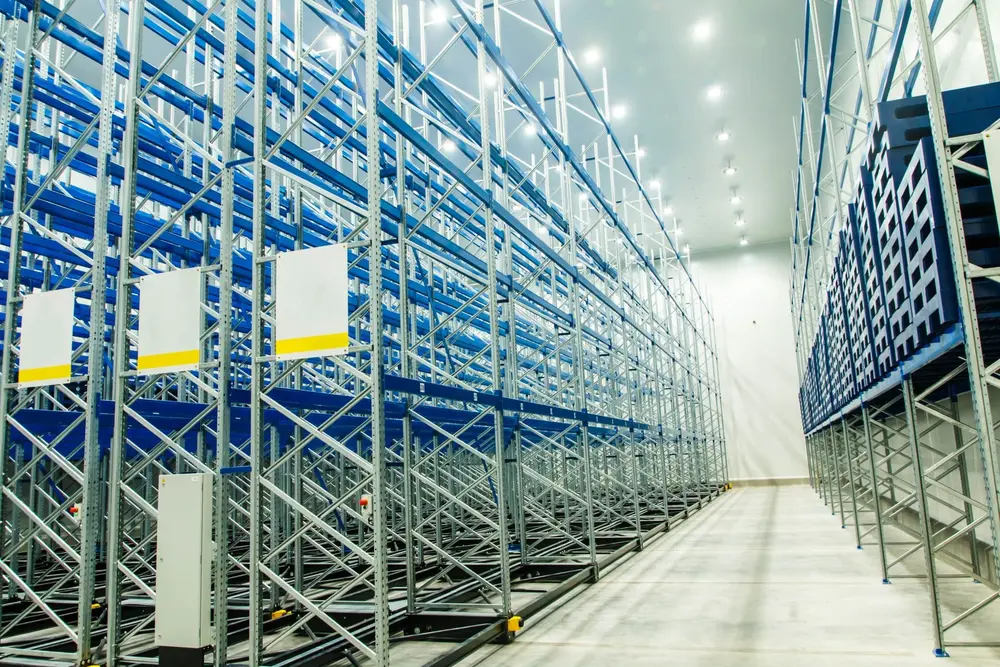
What Frozen Food 3PL solutions are available for businesses?
Maintaining the integrity of frozen products throughout the supply chain is crucial for businesses in the food industry, and that's where specialized third-party logistics (3PL) solutions come into play. At Lindner Logistics in Milwaukee, we offer a comprehensive range of frozen food 3PL solutions designed to keep your products at optimal temperatures from storage to delivery. Our temperature-controlled warehousing facilities are equipped with advanced refrigeration systems, ensuring your frozen goods, whether ice cream or frozen vegetables, remain fresh. We also provide specialized packaging solutions, such as insulated containers and dry ice, to protect your products during transit. Additionally, our refrigerated transportation services utilize trusted carriers with real-time tracking and temperature monitoring to guarantee safe delivery. With robust inventory management systems, we help streamline your stock levels and replenishment processes, minimizing stockouts. Partner with Lindner Logistics to navigate the complexities of frozen food logistics and keep your products frosty every step of the way. Ready to elevate your frozen food logistics? Contact us today!
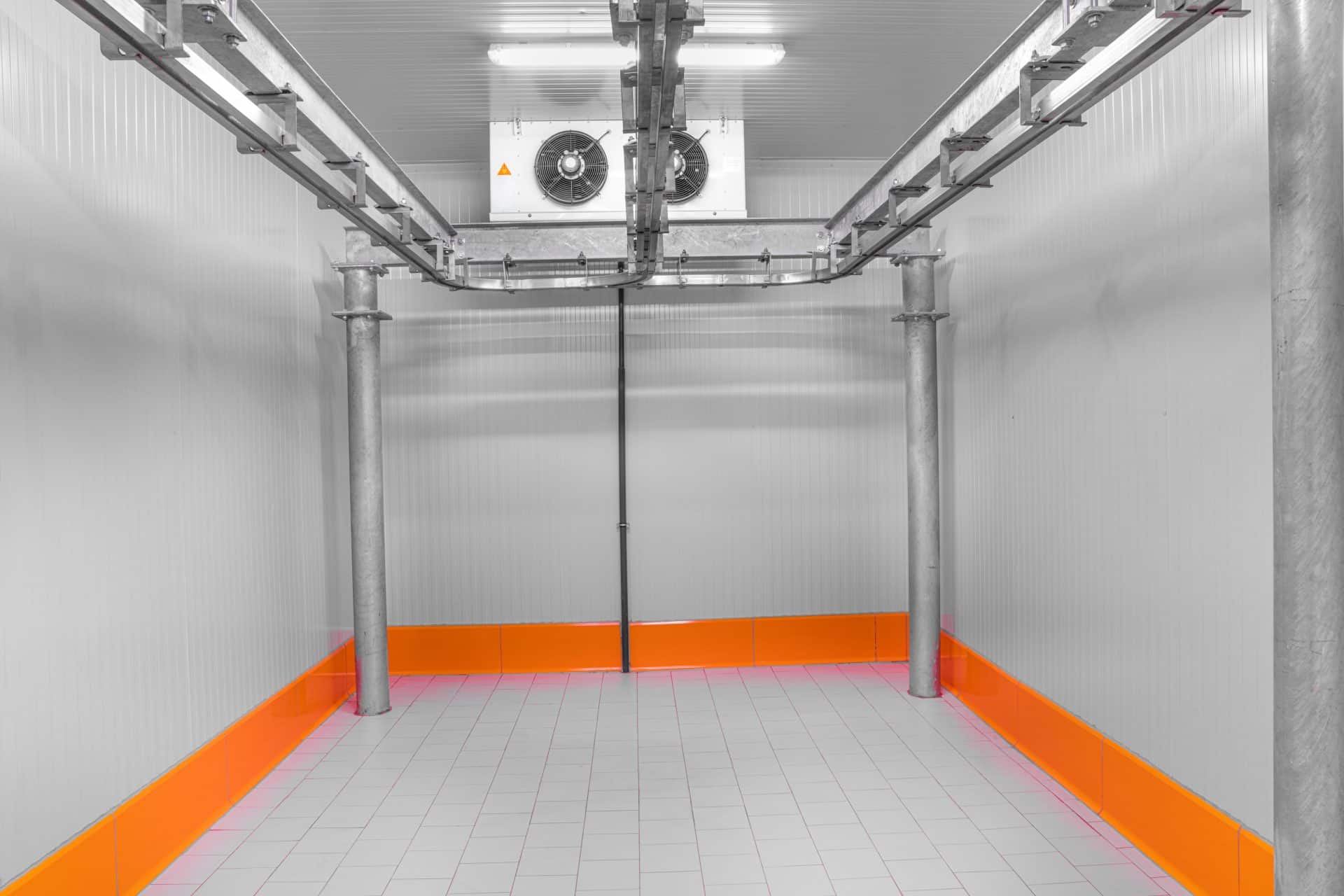
Freezer cold storage and 3PL integration
Integrating freezer cold storage with third-party logistics (3PL) services can dramatically enhance supply chain efficiency, especially for businesses handling temperature-sensitive products like perishables or pharmaceuticals. Lindner Logistics offers state-of-the-art freezer storage facilities, maintaining optimal temperatures to preserve product integrity. By consolidating both storage and logistics under one roof, we streamline operations, reducing errors and accelerating order fulfillment. This integration also provides real-time visibility into inventory and shipments, allowing businesses to stay agile and responsive. Our customized solutions, coupled with rigorous compliance and quality assurance standards, make Lindner Logistics a trusted partner for optimizing cold chain management.
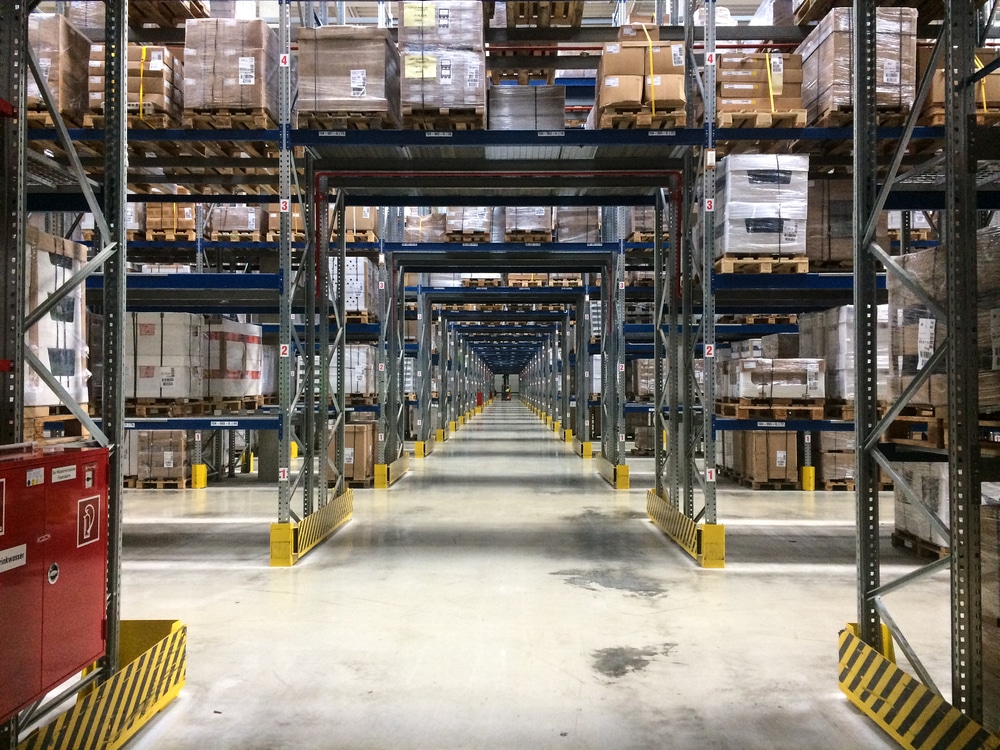
How to Ensure On-Time Delivery for Your Christmas Frozen Food Orders
Ensuring on-time delivery of Christmas frozen food orders is critical for B2B businesses during the holiday season. Strategic planning, including identifying necessary food items and placing orders early, helps avoid delays. Building strong relationships with reliable suppliers is essential to ensure timely deliveries, while negotiating clear shipping terms minimizes misunderstandings. Effective communication throughout the process keeps your business informed and ready to address potential issues. Monitoring external factors like weather, leveraging local suppliers for faster deliveries, and implementing quality checks upon receipt help maintain product standards and client satisfaction. With these strategies in place, businesses can deliver a seamless holiday experience.
Frequently Asked Questions
What is WORCS and how does it support warehouse management?
WORCS (Warehouse Operations Real-time Control System) is Lindner Logistics' proprietary WMS designed to improve visibility, inventory accuracy, and operational efficiency across all warehousing services in Wisconsin.
How does Lindner’s WMS help optimize warehouse space in Wisconsin?
Lindner uses advanced WMS technology solutions to analyze inventory flow and storage density, helping businesses maximize warehouse space in facilities across Waukesha, Milwaukee, and the Midwest.
Can WORCS track frozen and food-grade inventory in real time?
Yes. WORCS supports frozen 3PL and food-grade warehouse operations by offering real-time inventory tracking, batch/lot control, and temperature-sensitive compliance.
What are the benefits of implementing a warehouse management system (WMS)?
A WMS enhances inventory accuracy, speeds up fulfillment, reduces labor costs, and improves customer satisfaction. Lindner’s warehouse management system is designed to support dry storage, freezer storage, and ecommerce fulfillment.
Is WORCS compatible with ecommerce platforms?
Absolutely. WORCS integrates seamlessly with ecommerce warehouse management systems to automate order processing and streamline multi-channel fulfillment operations in Wisconsin.
What features should I look for in a 3PL WMS system?
Key features include real-time visibility, barcode scanning, order automation, inventory forecasting, and reporting. Lindner’s WMS platform supports 3PL warehouse operations for diverse industries in the region.
How does Lindner Logistics ensure inventory accuracy with WMS?
Using barcode scanning, automated workflows, and cycle counts, Lindner’s WMS helps maintain high levels of inventory accuracy across food-grade, dry, and refrigerated storage facilities.
Can your WMS handle value-added services like kitting and labeling?
Yes. Lindner’s warehouse management system tracks value-added logistics services such as kitting, custom labeling, and product repacking, ensuring full traceability and reporting.
Where are Lindner's WMS-enabled warehouses located?
Lindner Logistics operates WMS-powered warehouses in Waukesha, Milwaukee, and other key locations in Wisconsin, offering cold storage, dry goods warehousing, and 3PL fulfillment.
How does WORCS support compliance in food-grade warehousing?
WORCS enables traceability, FIFO/FEFO logic, and temperature monitoring - essential for food-grade warehouse requirements and frozen food logistics in Wisconsin.